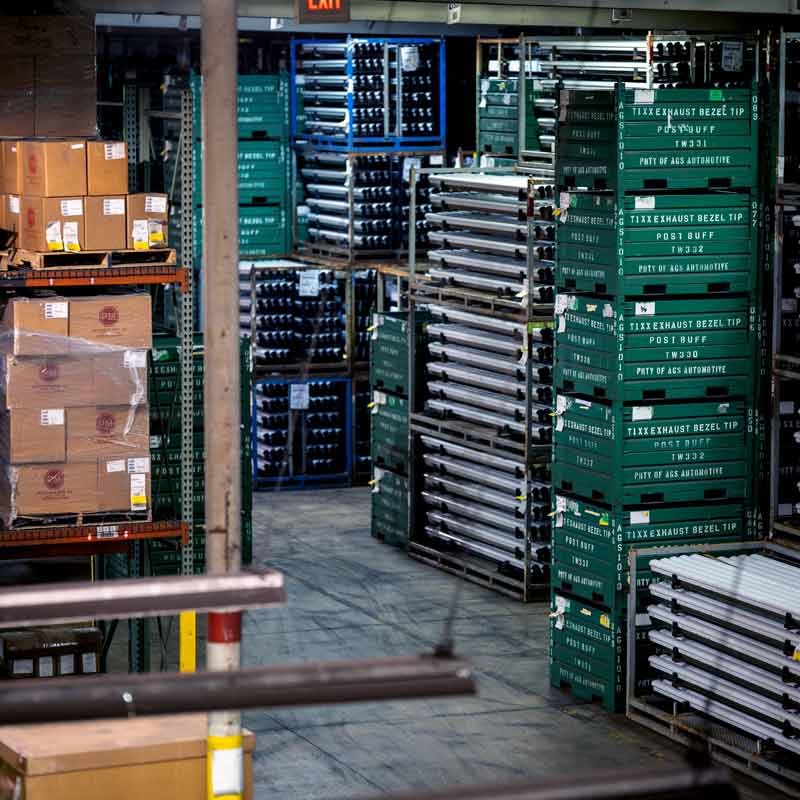
Allied Finishing
Glossary
- What is Chrome Plating?
Chrome plating (or chrome electroplating/dipping as some people refer to it) is an electrolytic process that deposits chromium metal onto a plastic or metal surface. It is most commonly used for aesthetic and/or corrosion prevention applications. - What is Polish and Buff?
Polish and Buff is a prefinishing process that is used to prepare the substrate for the plating process. This process is used to achieve a smooth finish on the part, prior to plating, and eliminate the potential for pits, nicks, dings, and other defects that may be in the part.Unfortunately the chrome plating process alone will not hide or fill in any defects that are in the substrate; in fact, after plating it will only make them more visible. This is the main reason why a polish and buff operation is required prior to chrome plating for cosmetic components.
- What is Copper Buff?
Copper Buff is a process that is mainly associated with die castings that require extremely high cosmetic standards. Since die castings by nature tend to be quite porous, it can be difficult to achieve certain high cosmetic standards from a polish and buff application alone.Therefore, a heavy layer of copper is applied and the part is buffed once again. The main goal is to “massage” and move the copper around to fill in any pits, holes, etc. that may be visible, and allow for a smooth final finish.
- What is Rack Plating?
Rack Plating is the process of fixating/hanging a part on a rack (via clips) in order to achieve proper plating needs. This process is most often used for parts that may have certain plating thickness criteria, aesthetic requirements, or may be too large for a barrel plate application. - Decorative Chrome vs. Hard Chrome
The main difference between decorative chrome and hard chrome lies within the applied layer of chrome itself. Hard chrome applications will contain a heavy layer of chrome (typically measured in the thousandths of an inch), whereas decorative chrome will contain a very thin layer of chrome (typically measured in the millionths of an inch) with the majority of the thickness actually being copper and/or nickel.In addition, hard chrome plating processes typically are used on components made of steel, and mainly serve for wear resistance purposes. Decorative chrome plating processes can also serve as a functional coating, but mainly are tied to applications that require a more aesthetically pleasing finish.
- Hexavalent Chrome vs. Trivalent Chrome
The elemental difference between hexavalent and trivalent chromium lies within their chemical makeup, and thus gives them different oxidation states. Aside from this, there are many advantages and disadvantages to each process. For example, trivalent chrome has better coverage in lower current density areas of a part, but it is also a much more expensive plating process to maintain. Hexavalent chrome provides a more consistent “blueish” color that is most commonly expected and desired, but it is also more hazardous to one’s health in its liquid state.As it stands today, the main distinguishing difference between these two finishes still lies within the color variance. While some markets and regions of the world are making a push for trivalent chrome (due to environmental reasons), it does not achieve the blueish tint that is desired in a decorative chrome plating part. The vast majority of markets such as Automotive, Motorcycle, Heavy Truck, Medical, Appliance, etc. are still using hexavalent chromium solely because of the desired color it produces.
INTERESTED IN WORKING WITH ALLIED FINISHING?
Send us a message or give us a call. We are here to help!